Why Modern Powder Coating Ovens Use Smart PLC Controls
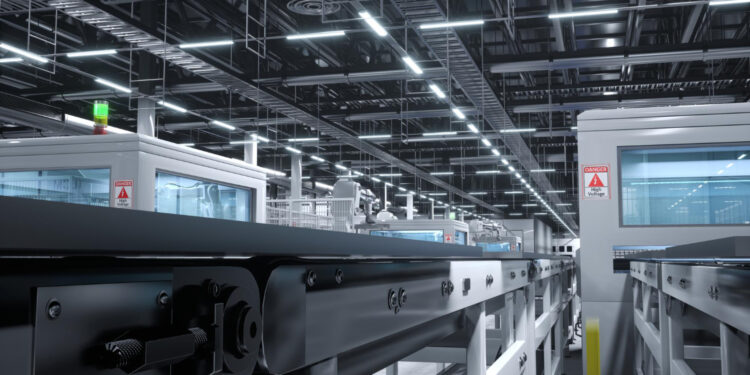
Manufacturers demand precision when it comes to powder coating. A flawless finish depends on temperature consistency, airflow control, and real-time adjustments. Modern powder coating ovens use smart PLC controls to achieve these standards, ensuring smooth operation, efficiency, and quality. These systems bring automation, safety, and customization to the coating process, making them indispensable for achieving professional results.
Instant Heat and Airflow Tweaks Maintain the Perfect Balance for Smooth, Even Curing
Achieving an even, durable finish in powder coating ovens depends on precise temperature and airflow regulation. Too much heat can lead to discoloration or over-curing, while inconsistent airflow results in an uneven coating. Smart PLC controls manage these variables by making real-time adjustments, ensuring that every part of the coated object receives the same level of heat. This technology eliminates manual intervention and prevents common curing problems that lead to rework.
Powder coating ovens equipped with smart controls constantly monitor internal conditions and tweak heat distribution instantly. These systems detect minor fluctuations and correct them before they affect the final finish. By optimizing airflow and temperature simultaneously, PLC-driven ovens prevent uneven curing, reduce energy waste, and increase efficiency. With this level of precision, manufacturers get uniform coatings every time, without guesswork or manual recalibration.
Intelligent Automation Takes the Guesswork out, Delivering Flawless Results Every Time
Traditional ovens rely on manual settings that leave room for human error, while smart PLC controls take the uncertainty out of the powder coating process. These systems are programmed to maintain exact curing conditions, adjusting as needed to ensure consistent results. Once an operator sets the desired parameters, the system maintains them with minimal input, reducing the risk of errors.
Modern powder coating ovens use automation to adapt to different coating requirements without requiring constant supervision. The PLC system detects inconsistencies in temperature, airflow, or curing time and corrects them instantly. This ensures that every batch meets the same high-quality standard, eliminating wasted materials and time-consuming touch-ups. Automation also enhances productivity by allowing operators to handle multiple tasks while the system takes care of maintaining the perfect curing environment.
Built-in Safety Sensors Catch Overheating and System Hiccups Before They Become Big Problems
Powder coating ovens operate at high temperatures, making safety a priority. Overheating, equipment malfunctions, or airflow blockages can lead to serious damage if left unchecked. Smart PLC controls come equipped with built-in safety sensors that monitor the oven’s performance and detect potential hazards before they escalate into costly failures.
These sensors constantly scan for irregularities, such as rising temperatures beyond safe limits or blockages in the ventilation system. When an issue is detected, the PLC system either corrects the problem automatically or alerts the operator immediately. This level of oversight minimizes downtime, reduces the risk of equipment damage, and prevents accidents. By integrating safety features directly into the control system, modern powder coating ovens enhance reliability and protect both workers and equipment.
Customizable Controls Let Operators Fine-tune Settings for Different Coating Needs
Different coatings require different curing conditions, and a one-size-fits-all approach doesn’t always work. Smart PLC systems offer customizable controls that let operators fine-tune settings based on the type of powder, thickness of the coating, and material being treated. Instead of relying on preset temperatures and curing times, operators can program precise parameters tailored to each job.
With customization options, manufacturers can ensure that each project gets the exact amount of heat and airflow needed for a perfect cure. Whether working with heat-sensitive materials or high-temperature coatings, the ability to adjust settings prevents errors and enhances finish quality. These controls also allow operators to create and save multiple curing profiles, making repeat jobs easier and more consistent.
User-friendly Touchscreens Simplify Operation, Cutting down on Mistakes and Training Time
Operating advanced powder coating ovens doesn’t have to be complicated. Smart PLC controls often come with touchscreen interfaces that make them easy to use, even for those with minimal experience. Instead of navigating through complex control panels, operators can adjust settings with a few taps on a screen. This streamlined interface reduces the likelihood of input errors and speeds up the learning process for new team members.
With intuitive touchscreen navigation, operators can quickly access real-time data, make adjustments, and monitor performance without guesswork. These displays provide clear feedback on temperature, airflow, and curing status, ensuring that operators always know what’s happening inside the oven. A simplified control system means fewer mistakes, shorter training periods, and more efficient production.
Remote Monitoring Allows Real-time Adjustments Without Being Tied to the Control Panel
Manufacturing floors are busy environments, and operators can’t always stand next to the oven to monitor curing cycles. Smart PLC controls solve this problem by enabling remote monitoring, allowing operators to track and adjust oven performance from anywhere. Whether using a tablet, smartphone, or computer, real-time data is accessible without being tied to the control panel.
This remote capability improves efficiency by reducing unnecessary downtime. Operators can receive alerts if temperatures fluctuate, airflow changes, or a potential issue arises. Adjustments can be made instantly, ensuring that production stays on schedule. Remote access also allows supervisors to oversee multiple ovens at once, making large-scale operations more manageable.