Innovative Trends in Injection Molding and Tooling
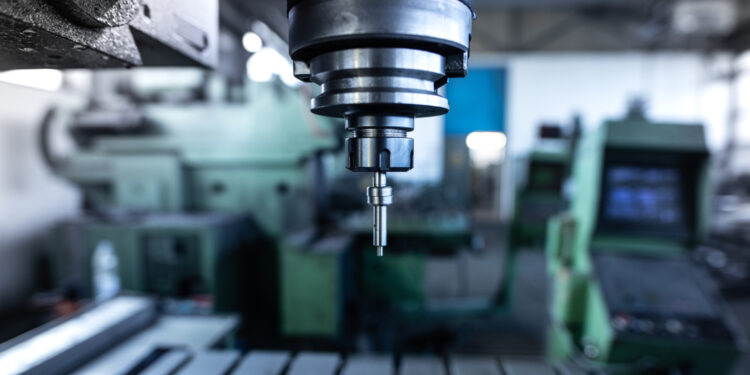
Key Takeaways:
- Learn about the newest developments influencing injection molding and tooling in the future.
- Understand how technological advancements impact the manufacturing industry.
- Explore the benefits of automation and sustainable practices.
- Learn about the challenges and opportunities in modern tooling processes.
Advancements in injection molding and tooling focus on automation, sustainability, and precision. Smart manufacturing integrates AI and IoT for real-time monitoring, enhancing efficiency. Sustainable materials and energy-efficient processes reduce waste. Rapid prototyping and 3D printing accelerate design iterations, driving innovation and cost-effective production in modern manufacturing.
Table of Contents
Introduction
Few areas see as much transformation as injection mold tooling in the ever-evolving manufacturing landscape. Integrating state-of-the-art techniques redefines efficiency, quality, and speed in production processes. As industries strive for higher standards, these avant-garde methods empower businesses to produce superior components swiftly and reliably, all while minimizing costs and maximizing output.
This sea change in manufacturing isn’t confined to merely enhancing volume and precision. It represents a holistic improvement across the production domain, including a firm commitment to sustainable practices. Engaging in these contemporary approaches is critical for companies yearning to stay competitive and contribute positively to the environment.
Technological Advancements in Injection Molding
Technological advancements are ushering the injection molding sector into a new era in what can only be described as an industrial revolution. With the aid of cutting-edge technologies, production floors are becoming increasingly automated. This move towards robotics and innovative technologies reduces the likelihood of human error and drastically boosts productivity levels. Such advancements allow businesses to deliver high-quality products that meet or exceed consumer expectations.
These evolving technologies are more than just tools; they’re essential catalysts for operational excellence. They enable precise control over the manufacturing capabilities, offering companies the agility to respond swiftly to market demands by altering production scales seamlessly. This adaptability makes lean manufacturing techniques that concentrate on cutting waste and inefficiencies possible, essential for preserving a competitive edge.
The Rise of Sustainable Practices
In a world increasingly aware of its environmental impact, the rise of sustainable practices within the injection molding industry is a crucial development. The commitment to eco-friendly methods is not just a response to societal pressures; it’s a strategic endeavor that crafts both environmental and economic benefits. By integrating recycled materials and optimizing resources, manufacturers can reduce their carbon footprint while often reducing overall costs.
The shift toward sustainability doesn’t end with material choices. Process improvements aimed at energy efficiency and waste reduction are also pivotal. Such green initiatives can significantly enhance a company’s reputation, appealing to environmentally conscious consumers and partners. Sustainable practices are a win-win scenario, promoting planet preservation while driving bottom-line results.
Automation in Tooling Processes
Automation is fast becoming the backbone of modern tooling processes. Integrating sophisticated machinery and software speaks to a future where manual intervention is minimized and precision is paramount. Automated systems can extend operational hours without incurring additional manpower costs, vastly reducing production times and improving cost-effectiveness.
The precision and consistency afforded by automation cannot be overstated. It allows for creating intricate and tailored designs that meet diverse customer needs while maintaining a high standard of accuracy. This capability propels businesses into a realm where mass production is seamlessly paired with customization, a combination increasingly demanded by today’s discerning clientele.
3D Printing: Transforming Tool Production
Among the most groundbreaking innovations in tooling is 3D printing. This technology enables crafting complex tools and prototypes that were once deemed too intricate or costly to create. With 3D printing, manufacturers witness reduced time and resources required to go from concept to execution. This agility fosters rapid innovation and allows for bespoke solutions tailored to specific client requirements.
Beyond prototyping, 3D printing supports small-scale production runs that push the boundaries of traditional manufacturing. Companies can now explore new design possibilities without the risk of investing heavily in conventional tooling. These capabilities open new doors for experimentation and originality, driving progress in ways not previously possible.
Challenges Facing the Industry
Despite these promising advances, the injection molding industry grapples with several challenges. The initial costs associated with upgrading to new technologies can be prohibitive for smaller players. Furthermore, the specialized skills required to operate and maintain this advanced equipment demand a dedicated investment in workforce training.
However, these challenges also present growth opportunities. Companies can mitigate these barriers by developing strategic training programs and seeking collaborative partnerships. For companies looking to fully utilize contemporary tooling techniques, such investments are essential to long-term success and industry leadership.
Future Opportunities in Injection Molding
With challenges come unprecedented opportunities that promise to reshape the future of injection molding. As companies continue to integrate innovative manufacturing technologies and adopt sustainable practices, they’re well-positioned to tap into emerging markets and customer segments. This alignment with green technology and digital innovation sets the stage for pioneering breakthroughs that could alter the entire product lifecycle.
Furthermore, fostering a continuous improvement and innovation culture unleashes the potential for growth and transformation in production capabilities. By capitalizing on these future opportunities, the injection molding industry stands ready to play a defining role in the next industrial age.
Conclusion: Embracing the Future of Tooling
The injection molding and tooling industry is advancing rapidly due to technological and sustainable initiatives. Companies are setting the standard for the future of manufacturing by adopting eco-friendly practices and advanced automation tools. Continuous innovation and adaptation are crucial for long-term success and growth in this dynamic industry.