9 Tips for Managing a Warehouse More Efficiently
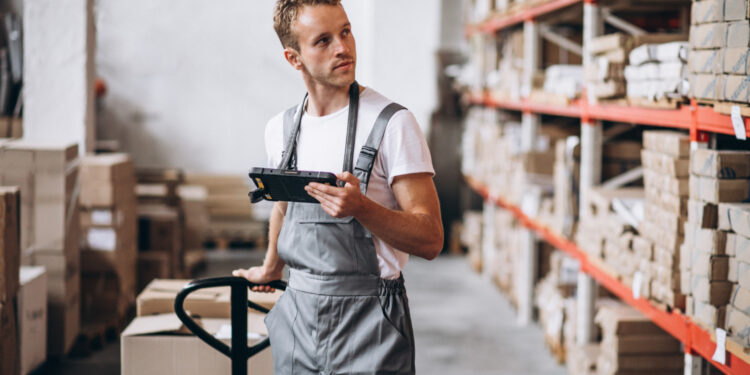
Running a warehouse is all about keeping things moving—literally. From streamlining workflows to minimising delays, every decision impacts overall efficiency. If operations feel slow or disorganised, it’s time to make changes that improve productivity, reduce costs, and optimise space. These nine strategies will help you run a more efficient warehouse without unnecessary complexity.
Table of Contents
- 1 1. Hire Forklifts Instead of Buying to Reduce Costs
- 2 2. Reorganise Your Warehouse Layout for Better Flow
- 3 3. Implement an Inventory Management System
- 4 4. Use Technology to Speed Up Order Processing
- 5 5. Keep Your Warehouse Organised to Prevent Delays
- 6 6. Train Staff Regularly for Maximum Productivity
- 7 7. Improve Picking and Packing Workflows
- 8 8. Prevent Equipment Downtime with Regular Maintenance
- 9 9. Use Data to Continuously Optimise Performance
- 10 Small Changes, Big Impact
1. Hire Forklifts Instead of Buying to Reduce Costs
Forklifts are essential in any warehouse, but owning them outright might not be the smartest financial move. Forklift hire Melbourne instead offers flexibility, allowing you to scale up during peak seasons and avoid high maintenance costs. It also means you’re not stuck with outdated equipment—rental providers ensure their machines are regularly serviced and up to standard. This approach cuts down on unexpected expenses and ensures you always have the right tools for the job.
2. Reorganise Your Warehouse Layout for Better Flow
An inefficient layout can slow down picking, packing, and movement, leading to wasted time. If workers are constantly navigating around obstacles or taking long routes, it’s worth rethinking how space is used. Arrange fast-moving stock closer to packing areas, keep aisles clear, and ensure there’s a logical flow that reduces unnecessary walking. The right layout can significantly speed up daily tasks and improve safety.
3. Implement an Inventory Management System
Tracking stock manually or relying on outdated spreadsheets increases the risk of errors and inefficiencies. A modern inventory management system helps keep stock levels accurate, automates reordering, and integrates with warehouse management software. This means fewer delays, better stock forecasting, and improved overall operations.
4. Use Technology to Speed Up Order Processing
Manually recording stock and scanning items at multiple checkpoints adds unnecessary delays. Investing in barcode scanners or RFID tracking speeds up order processing and improves accuracy. These systems automatically update inventory in real-time, reducing human error and preventing issues like overselling or misplaced stock.
5. Keep Your Warehouse Organised to Prevent Delays
A cluttered warehouse is an inefficient one. Disorganised storage slows down order fulfilment and increases the risk of accidents. Keeping everything tidy ensures a smooth workflow. Here’s how to maintain an organised warehouse:
- Introduce a ‘clean as you go’ system – Encourage workers to tidy up during shifts instead of letting clutter pile up.
- Maximise vertical space – Use high racking and shelving to keep floors clear.
- Standardise labelling – Clearly label shelves, bins, and sections to make it easier to find stock.
- Remove obsolete stock – Regularly audit inventory and clear out slow-moving or redundant products.
- Assign specific storage zones – Group similar items together so workers spend less time searching for them.
A well-organised warehouse saves time, reduces stress, and improves efficiency across all operations.
6. Train Staff Regularly for Maximum Productivity
Even with the best systems in place, an untrained workforce can slow things down. Regular staff training ensures that employees understand best practices, safety procedures, and how to use warehouse technology effectively. Well-trained workers make fewer mistakes, work faster, and contribute to a safer and more efficient workplace.
7. Improve Picking and Packing Workflows
Picking and packing errors lead to delays, returns, and unhappy customers. Streamlining these processes boosts efficiency and reduces wasted time. Methods like batch picking (where multiple orders are picked simultaneously) and zone picking (assigning workers to specific sections) can dramatically cut down order fulfilment times. Packing stations should also be well-organised, with all necessary materials easily accessible to speed up the process.
8. Prevent Equipment Downtime with Regular Maintenance
Warehouse equipment failures can bring operations to a halt. Rather than waiting for a breakdown, scheduled maintenance keeps everything running smoothly. Create a maintenance schedule for forklifts, conveyor belts, and pallet jacks, ensuring regular servicing and inspections. Preventative maintenance reduces the likelihood of unexpected repairs, keeping productivity high and avoiding costly downtime.
9. Use Data to Continuously Optimise Performance
The best way to improve efficiency is to track what’s working and what’s not. By using warehouse management software, you can monitor key performance indicators (KPIs) like picking accuracy, stock turnover, and order fulfilment times. This data helps identify bottlenecks and opportunities for improvement, allowing you to make informed decisions that keep operations running at peak efficiency. Over time, these optimisations will not only save money but also create a safer, more productive work environment.
Small Changes, Big Impact
Warehouse efficiency isn’t about making one big change—it’s about refining multiple small processes to create a smooth-running system. Whether it’s hiring forklifts instead of buying, reorganising stock placement, or investing in better technology, every improvement adds up. By implementing these strategies, you’ll increase productivity, reduce costs, and make warehouse management more efficient than ever.