What Does a VDF Pump Do
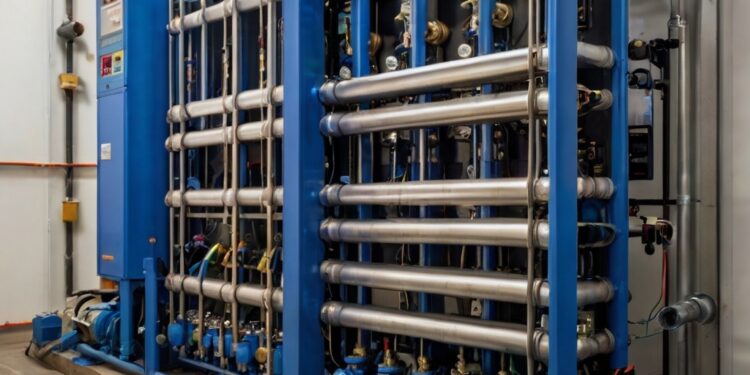
Pumping systems use nearly 20% of the world’s electric motor energy. Some industrial facilities spend up to 50% of their electrical usage just on pumping operations. The high energy footprint makes VFD pump systems vital for modern industrial operations. Most existing pumping systems are oversized by more than 20%.
VFD pumps showed remarkable improvements in efficiency. Many installations achieve 30% to 50% energy savings. A San Francisco refinery saved 500,000 kWh monthly after adding VFDs and saved $750,000 annually. But despite these benefits, many engineers still make significant mistakes in VFD system design and implementation. This detailed guide gets into the common errors in VFD pump applications and provides solutions to achieve optimal system performance.
Table of Contents
- 1 Common VFD Pump Engineering Mistakes
- 2 Critical VFD Working Principles Often Misunderstood
- 3 Variable Frequency Drive Pump Implementation Errors
- 4 Advanced Troubleshooting for VFD Water Pumps
- 5 Here are some FAQs about the VFD pump:
- 5.1 What is a VFD for a pump?
- 5.2 What is VFD and why it is used?
- 5.3 What is the difference between VSD pump and VFD pump?
- 5.4 When should you use a VFD?
- 5.5 Do I need a pressure tank with a VFD pump?
- 5.6 Can a VFD stop a motor?
- 5.7 Are VFDs bad for motors?
- 5.8 What is the minimum speed for a VFD pump?
- 5.9 What are the disadvantages of VFD?
Common VFD Pump Engineering Mistakes
Engineering mistakes in VFD pump installations can lead to substantial operational inefficiencies and system failures. Your original understanding of these common errors helps prevent equipment damage and the system from getting pricey downtime.
Incorrect VFD sizing calculations
VFD pump performance depends on proper sizing. You just need to derate the output current by 50% to size drives correctly. Engineers often look at horsepower ratings but miss current requirements. Matching the VFD size to the AC induction motor is vital, and current remains the most significant parameter.
Normal Duty VFDs work best with variable torque applications like centrifugal pumps. Heavy Duty VFDs are built for constant torque applications. Using a Heavy Duty VFD for normal duty tasks will only add extra costs to your projects.
Poor harmonics management
VFD pump systems face a big challenge with harmonics management. These nonlinear waveforms create voltage distortion across reactors that can affect transient performance negatively. Here’s what happens when you have harmonic problems:
- Overheating of transformers and motors
- Incorrect operation of electronic instruments
- Excessive current in power factor correcting capacitors
- Premature circuit breaker failure
An 18-pulse converter gives maximum efficiency for motors over 50 hp. Smaller loads work well with an inductor or passive filter for harmonic mitigation. System longevity depends on how well you manage harmonics.
Improper cable selection and routing
Cable choices and routing substantially affect VFD pump performance. You can use single wire conductors, but shielded power cable works better for both input and output cables. Smart routing keeps input wires away from output wires to avoid interference.
Power wires should stay at least one inch apart when running parallel. Any crossing should happen at 90-degree angles. Control wiring needs about 2 inches of space from high voltage wiring. The system performs best and has minimal electromagnetic interference when you properly shield and ground connections at both ends.
Critical VFD Working Principles Often Misunderstood
Understanding how variable frequency drive pumps work is vital to system performance. Engineers often misunderstand basic VFD operations. This leads to poor implementations.
Fundamental operation misconceptions
Engineers commonly misunderstand VFD output characteristics. The output waveform that goes to motor windings isn’t sinusoidal, which many people believe. VFDs actually rectify three-phase input to fixed DC voltage and then invert it. This creates variable voltage and frequency outputs. IGBT pairs control current flow through precise switching patterns.
Voltage and frequency must maintain a linear relationship to keep torque constant. The V/f ratio determines the motor’s magnetic field strength. Output frequency and voltage should increase at similar rates to keep motor flux constant for the best performance.
Speed-torque relationship errors
Speed limitations in VFD pump applications need more attention from engineers. TEFC motors shouldn’t run at full load below 15 Hz because of cooling limits. The highest safe operating speed depends on mechanical limits like bearings and balance.
Torque control creates another common problem. VFDs in torque mode adjust power and speed to reach commanded torque. The motor’s back-EMF increases with speed. This makes the VFD supply more voltage to maintain current flow. Torque reduces proportionally with rising speed once the VFD hits maximum voltage output.
Control loop configuration mistakes
Stable VFD pump operation needs proper closed loop control. The system compares actual pressure values with desired setpoints and adjusts pump speed. Stability problems usually start from wrong error signal processing.
These elements matter in control loop setup:
- Proportional gain affecting system response
- Integral time for error correction
- Speed limitation parameters preventing runaway conditions
Proper tuning of these parameters leads to success. Systems often become unstable from too much proportional gain or wrong integral time settings. Engineers should confirm control loop performance through systematic testing before deployment.
Variable Frequency Drive Pump Implementation Errors
VFD pump installations require careful attention to detail. More than 50% of VFD failures happen because of improper installation and startup procedures. This makes it significant to learn about common implementation mistakes.
Installation location oversights
VFD pump system placement needs more than simple mounting requirements. Wall-mounted units depend on a ‘chimney effect’ to cool heat sinks and work best against smooth, flat, vertical surfaces. Systems installed above 3,300 feet altitude need 2% derating for every 1,000 feet to maintain performance.
Engineers must avoid installing VFD units in these locations:
- Mezzanines with unpredictable temperature variations
- Areas exposed to direct sunlight
- Locations near external heat sources
- Spaces with inadequate ventilation clearance
Cooling system design flaws
Heat management is a vital challenge because VFDs convert electrical energy into mechanical energy and generate substantial heat. Most VFD installations have a maximum ambient temperature threshold between 104°F and 125°F.
Free-standing variable frequency drives need specific minimum clearances for proper airflow circulation. Larger units require adequate spacing around them for cooling. Poor ventilation can create “hot spots” on VFDs’ surface and interior, which can damage sensitive electronics.
Grounding and shielding issues
Grounding serves two key purposes: safety and common mode noise reduction. Modern drives’ higher switching frequencies increase common-mode voltages and currents. These discharge currents can erode bearings over time and lead to furrows or fluting.
Many installers forget to clean the motor’s feet during installation. Manufacturing overspray collects on the motor’s feet bottom, so thorough cleaning and grinding creates a low-impedance path to ground. Without direct connection between the drive and motor frame, inducted voltages often exceed NEMA’s acceptable standard of 300 millivolts on motor shafts.
The ground grid should provide a low impedance path for common mode noise currents to achieve optimal performance. Ungrounded components can accumulate electrical charges that exceed the safe touch potential of 50 volts.
Advanced Troubleshooting for VFD Water Pumps
You just need systematic analysis and deep technical understanding to fix variable frequency drive pumps. We focused on identifying and fixing complex problems by paying attention to specific operational parameters and system behaviors.
Here are some FAQs about the VFD pump:
What is a VFD for a pump?
A VFD (Variable Frequency Drive) for a pump is a device used to control the speed of the motor that drives the pump. It allows for precise adjustment of motor speed, improving energy efficiency, and optimizing the performance of systems like a VFD well pump, VFD water pump, or even a VFD pool pump. With VFD technology, the pump can operate at varying speeds depending on the demand, which leads to reduced wear and energy savings.
What is VFD and why it is used?
A VFD (Variable Frequency Drive) is used to control the speed and torque of electric motors by varying the frequency and voltage supplied to the motor. VFDs are commonly used in systems like pump VFDs to ensure optimal performance and efficiency. For example, in applications like a VFD pump, it provides more control over flow rates and helps to reduce power consumption.
What is the difference between VSD pump and VFD pump?
While VSD (Variable Speed Drive) and VFD (Variable Frequency Drive) are often used interchangeably, the main difference lies in how they control motor speed. A VFD pump adjusts the motor’s speed by changing the frequency of the electrical supply, whereas a VSD pump can be used to control various types of drives beyond just frequency. Both systems improve energy efficiency, but a VFD pump offers finer control, especially for water and pool pumps.
When should you use a VFD?
You should consider using a VFD whenever you need to control the speed of a motor to optimize performance, reduce energy costs, or extend equipment life. For example, a VFD well pump or VFD water pump can automatically adjust its speed depending on demand, providing efficient operation for applications like irrigation, water systems, and pools.
Do I need a pressure tank with a VFD pump?
While a pressure tank is not strictly necessary with a VFD pump, it can be beneficial depending on the application. For a VFD well pump or water system, a pressure tank helps to maintain a consistent water pressure. However, the VFD itself can regulate the speed of the pump, reducing the need for a pressure tank in some cases, but it depends on the specific requirements of your system.
Can a VFD stop a motor?
Yes, a VFD can stop a motor by reducing the frequency and voltage supplied to the motor until it is completely turned off. For example, a VFD pool pump or any other VFD pump can gradually decelerate a motor to stop it smoothly, avoiding sudden changes that could cause mechanical stress.
Are VFDs bad for motors?
No, VFDs are not inherently bad for motors. In fact, they can extend the life of motors by providing smoother acceleration and deceleration, as well as reducing energy consumption. Properly installed and configured VFDs for pumps, like a VFD water pump, ensure that motors run at optimal efficiency and reduce wear.
What is the minimum speed for a VFD pump?
The minimum speed for a VFD pump is determined by the motor and the pump’s application. For most systems, the minimum speed is typically set to ensure that the pump maintains a certain level of performance, like a minimum flow rate in a VFD water pump. Setting the speed too low can cause issues such as cavitation or inadequate pumping.
What are the disadvantages of VFD?
While VFDs offer many benefits, they can have some disadvantages. They can be expensive to install initially, and the complexity of the system may require regular maintenance. Additionally, a VFD pump, especially for well or water systems, may generate harmonic distortion that can affect the electrical system unless properly filtered.